A typical scenario that is familiar to every maintenance technician: a machine breaks down due to a defective component and the system needs to be restarted as quickly as possible. However, this can only happen if the right spare part is in stock and can be found quickly.
Given the enormous variety of spare and wear parts, it is physically (in terms of storage space) and economically (in terms of inventory management costs) impossible to keep all parts of the machinery in stock. It can therefore be expensive and time-consuming if a spare part is suddenly unavailable.
What challenges do maintenance teams face in spare parts management? Which new processes and tools support the MRO transformation?
"Manufacturers keep millions of spare parts in stock in their production networks without realizing that up to 50% of these parts have not been used in the last three years. This ties up capital and causes unnecessary storage and procurement costs. With the help of software solutions to optimize spare parts management, companies can unleash considerable savings and inventory potential."
Martin Weber
CEO | SPARETECH
Five well-known challenges in spare parts management
Today, maintenance professionals must rely on often fragmented, non-digitized MRO systems. As plant operators often work with multiple machine manufacturers and suppliers, the lack of transparency regarding common spare parts and their prices becomes a significant challenge. This fragmentation can lead to several consequences, including high machine downtime, increased procurement costs for (short-term) spare parts orders, and high inventories due to the accumulation of excess and 'just in case' spare parts.
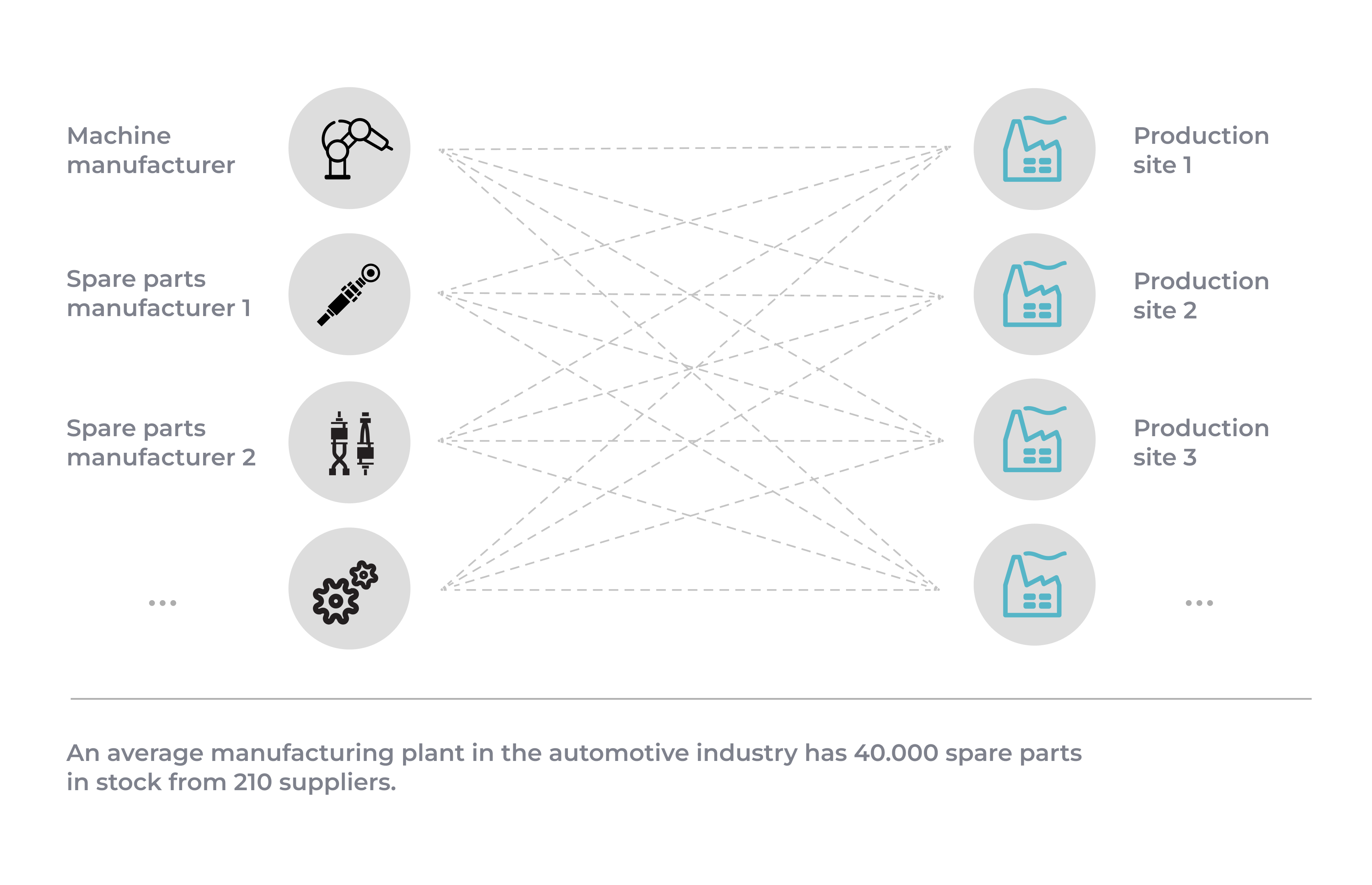
The challenges mentioned arise from problems that are often already known:
- Poor master data quality in the ERP system, including duplicates, incomplete entries, and outdated parts, among other incorrect data stored or entered into the system.
- High manual effort in identifying or creating spare parts leads to time-consuming tasks and human error.
- Lack of transparency about which parts are available in the company's production network.
- No transparency about existing procurement alternatives and the resulting higher procurement costs.
- Lack of internal process optimization that goes beyond the purchase of tools.
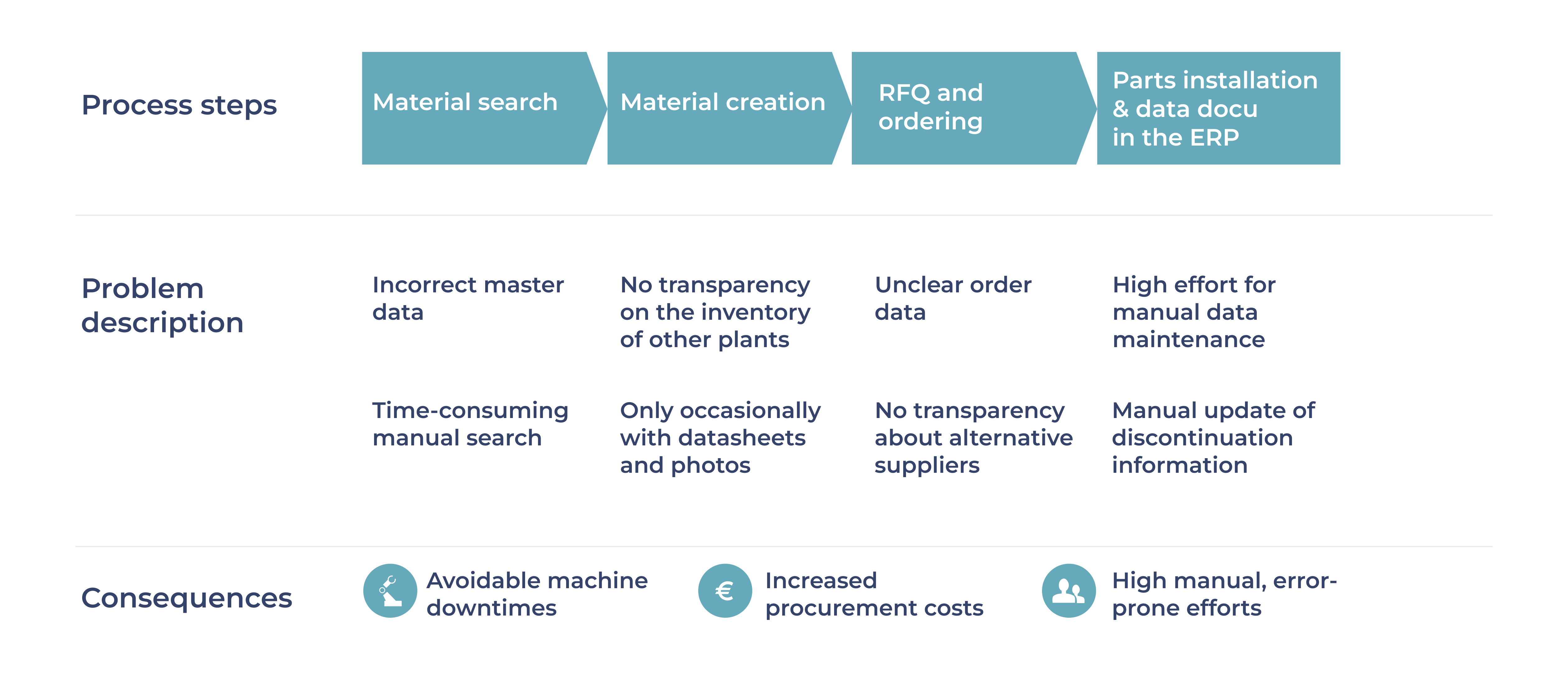
Problems in the spare parts management process and common causes
A classic situation: Poor master data quality in the ERP system
Suppose a spare part is needed due to a machine breakdown or the announcement of a breakdown (quality problem). To resolve the problem, you search for the required spare part in the ERP system (e.g. SAP) but cannot find it.
There may be various reasons for this:
- The part has never been created and ordered in the system
- The part was created incorrectly, e.g. typing error in the article number or type designation
- The search itself is carried out incorrectly, e.g. a typo in the article number or a typing error
Sad but true: humans are the actual cause of many potential sources of error. The actual bottleneck often lies at the very beginning: when a new machine is purchased, not all spare parts information (parts list) is initially transferred to the ERP system - either because manual creation would take far too long or because not all list items are considered relevant (e.g. parts that do not usually break).
However, if the part is created incorrectly, this can lead to slow-moving inventory, resulting in an unnecessarily overstocked warehouse with physically stored parts that are no longer in demand.
High manual effort
The high level of manual effort involved in spare parts management, be it when creating new materials or searching for the required spare parts in the event of a machine malfunction, is time-consuming and error-prone.
An average spare parts list contains 650 items, where a manual check can take up to 5 minutes per item. A single list can take up to two weeks to process. No wonder spare parts list checking is not a popular task in maintenance teams.
On the other hand, incomplete or even missing processing of these lists can lead to purchasing parts already in stock again, paying higher prices, and accumulating excess inventory, even though the required spare part may already be in the warehouse.
No transparency about fast and cost-effective sources of supply
After creating a spare part in the system, the next step is to find a cost-effective and reliable supply source.
Manual searches via internet platforms such as Google, Bing or eBay are time-consuming and mainly provide technical product information from the dealer. Many parts, especially from plant manufacturers, cannot be researched at all, which underlines the lack of data availability.
In addition, it is often not possible to assume that products here are inexpensive, as the highest-placed providers pay the most for ads and thus dominate the search results.
"Searching through countless manufacturer portals or waiting for a binding quote from customer service is not only time-consuming, but also costly - especially in the event of an unexpected malfunction when it comes to quickly finding the right spare part to get the machine up and running again."
Benedikt Weiss
Senior Customer Success Manager | SPARETECH
Lack of cross-location or cross-company cooperation for spare parts
The lack of cross-location information on the availability of spare parts in the production network is also a major problem. This problem is often due to IT barriers that hinder the effective exchange of information.
In addition, collaboration is hampered by the poor quality of the master data of all actors involved in the production network. Scaling effects in the company cannot be realized because the data is not made available, is not comparable, and is sometimes even incorrect.
Missing processes
Of course, many manufacturers know that they have problems. However, most lack the experience and processes to solve the problems that software alone cannot fix effectively - this challenge is common in IT projects. Therefore, the project scope should go beyond introducing new IT tools and include the development of new processes and their implementation through change management.
In some cases, a discrepancy arises at the responsibility level: between the decision-makers who see the value of standardizing and cleansing data and the maintenance staff and technicians who are responsible for implementation. A successful software implementation requires a considerable amount of manual effort on the part of the employees on site. Companies that take on this effort will benefit in the long run, while those that do not will often have to devote more resources to catching up.
Integration with customers' IT systems (APIs and ERP systems) is often challenging. Many software solutions offer API connections, but these have to be implemented by IT teams on the customer side, which is often an additional hurdle.
Digital solutions drive innovation in spare parts management
The good news is that it doesn't have to be that way!
Software solutions for spare parts management can tackle these challenges head-on, streamlining spare parts management and increasing efficiency.
⚙️ Automated master data management
Modern software tools can automate the maintenance of master data and thus ensure accuracy by continuously detecting and correcting errors such as duplicate or outdated entries. By integrating directly into ERP systems, these solutions ensure high data quality without the need for manual intervention.
SPARETECH frees your team from tedious administrative work with automated BOM checks for new machines, proactive obsolescence notifications and continuous ERP master data management.
⚙️ Streamlined spare parts sourcing
With centralized databases, software solutions, and access to a network of suppliers, the procurement of spare parts can be significantly faster and more efficient. These solutions offer automated comparisons of supplier options based on prices, delivery times, and reliability, enabling faster and more cost-effective procurement decisions.
SPARETECH helps procurement teams by giving them transparency and visibility on potential compatible parts, suppliers, and purchase prices.
⚙️ Cross-location portfolio transparency
Maintenance software solutions provide a unified view of spare parts availability across multiple locations, breaking down internal silos and enabling better resource allocation.
SPARETECH makes it possible to achieve synergies between production and third-party locations thanks to MRO transparency.
⚙️ Integration into existing systems
These software tools are designed to integrate seamlessly with existing IT infrastructure, including ERP systems. Flexible APIs enable smooth data exchange and ensure that the new software improves rather than disrupts ongoing operations. This integration helps companies leverage their existing investments while introducing more efficient processes.
Find out more about SPARETECH API and the data exchange options between SPARETECH and ERP systems.
"Software tools are not a "magic bullet" that automatically solves all problems related to spare parts. Success requires active use and effort, like buying a gym membership, which does not guarantee fitness without exercise. We observe how our successful customers use SPARETECH to optimize their spare parts management processes to achieve the best results. These insights are incorporated into the app in the form of helpful functions."
Thomas Karbe
Product Manager | SPARETECH