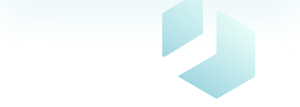
Eliminate manual work in spare parts management
Efficient maintenance processes are key to achieving operational excellence. By eliminating manual work in spare parts management, you can streamline your operations, reduce costs, and enhance productivity. Automated solutions and digital tools empower your team to quickly access, source, and procure spare parts with ease, saving valuable time and resources.








Time-consuming and inefficient processes in maintenance
Traditional ERP systems offer frustrating search experiences, requiring users to know specific properties like the article number. If this information is not at hand or the material master set is incorrect, users often don't find the spart parts even though they have it in stock.
Checking spare parts lists manually can be a time-consuming task, that takes up to 2 weeks net working time for a single person. Neglecting the checks can lead to excessive inventory and machine downtime due to missing spare parts.
Adding new materials in the ERP system can be time-consuming, requiring to complete many form fields and check for duplicates. This manual process can take up to 20 minutes per part, making it an very inefficient task.
Maintainer and Purchasers often interact on with each other to find a supplier that offers fast availability to the best price. This is not easy, as manual internet searches are time-consuming and do not offer the needed transparency.
Stop searching. Start finding.
Search for manufacturers, technical attributes, article numbers and other features to easily find the spare part you need. Find the right spare parts across your plants and storage locations, as well as in the SPARETECH database, containing millions of product data sets from renowned global manufacturers. Enrich your search results with original manufacturer data like images and product status directly from our database.
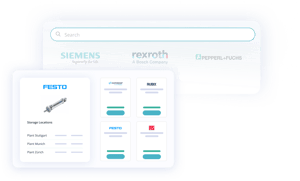
Gain efficiency with automated BOM & spare parts lists checks
Get your spare parts lists automatically checked by intelligent algorithms to identify duplicates and obsolescences in your material master. Additionally, your spare parts lists are matched against the SPARETECH database, enabling the auto-completion of your data with 100% reliable and up-to-date original manufacturer product information.
"SPARETECH checks all new spare parts lists automatically, which means an increase in efficiency of more than 50%. This is how digitalization works!"
/Marcus%20Strauss%20Portrait-1.webp?width=70&name=Marcus%20Strauss%20Portrait-1.webp 1x, https://144969486.fs1.hubspotusercontent-eu1.net/hub/144969486/hubfs/Portraits%20(internal%20%2B%20external)/Marcus%20Strauss%20Portrait-1.webp?width=105&name=Marcus%20Strauss%20Portrait-1.webp 1.5x)
Use verified data and avoid duplicates across all plants
SPARETECH’s fully digital workflow enables you to create new spare parts with ease. Pre-fill required fields with 100% correct and complete product information from the original manufacturer and prevent the duplication of existing materials through a live duplicate check against your material master. This way our clients reduce their manual efforts and shorten their process lead times massively.
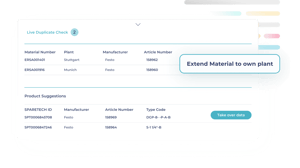
Over 200% efficiency gain for ElringKlinger using SPARETECH
Creating new materials within ERP systems is time-consuming, as it requires filling out multiple forms and fields with manual input. ElringKlinger has significantly increased their efficiency with SPARETECH. Form fields are now automatically pre-filled with 100% accurate data from our extensive product database, reducing the time to create a material by 277%.
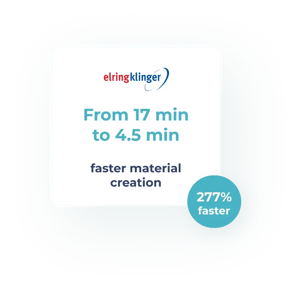
Get the best price with full supplier transparency
- Access 100% complete and up-to-date original manufacturer information.
- Easily compare procurement possibilities for identical parts.
- Ensure efficient cross-plant collaboration through one single source of truth and save unnecessary procurement costs and storage space.
Benefits of managing MRO master data with SPARETECH

Identify duplicates and obsolescence in the material master to sustainably reduce inventories.

Rely on a data-based approach so that the right part is available in the right place at the right time.
Compare procurement options of identical parts to achieve savings through substitutes and bundling effects.

Save yourself the online/catalog search and let the software create and update the master data within seconds.
Related to the topic
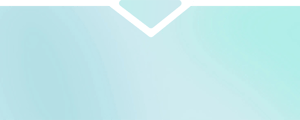
Get started today
SPARETECH is the fastest and most reliable way to reduce inventories and costs in spare parts management.