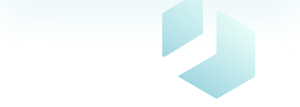
Clean master data with just a few clicks
Clean MRO master data is the basis of effective and efficient maintenance processes. With data from thousands of original manufactures and suppliers in one database and intelligent matching technologies, any material master can be analyzed for data enrichment, duplicates, and obsolescence within seconds.
How can master data be cleaned up easily?
Using SPARETECH, material master data cleansing becomes an easy process. In the first step, you upload your material master in the SPARETECH app which analyses all material master fields and automatically identifies duplicates, incorrect or incomplete data sets and discontinued materials. This happens with the help of SPARETECH’s intelligent matching algorithms which matches the data against a database covering tens of millions original manufacturer data sets.
1. Analyze and enrich your master data with SPARETECH
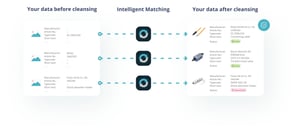
2. Identify duplicates in your master data
Cleansing data and especially removing duplicates from the system can be a lengthy process. Hence it is important to have a governance and support model in place. Removing duplicates is a collaborative effort and involves various stakeholders. Make sure everyone is on-board and understands the process. Get the full guide on how to find and remove duplicates in the material master.

3. Enrichment with original manufacturer information
Cleanse your inaccurate or faulty data with data enrichment suggestions from the SPARETECH database. Directly add missing information based on 100% correct manufacturer data with a material change request. No matter if you have missing or wrong information in the product name, product description, EAN, article number, type code, ECLASS IDs, or other fields – SPARETECH’s enrichment suggestions got you covered.
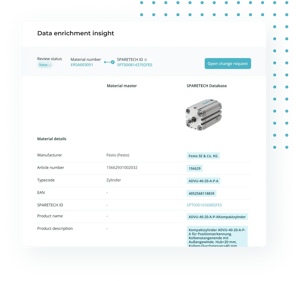
4. Ensure continuous data quality management
Companies often tend to focus solely on the initial cleansing of their master data. The three steps mentioned above enable you to get an accurate, consistent, and complete data basis. However, without continuous duplicate and quality checks during the new material creation process, duplicates and incorrect data may resurface the ERP System. Therefore, the fourth step of ensuring a duplicate- and error-free material creation process is essential to keep the master data clean.
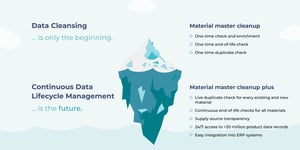
How does SPARETECH work in your daily operations?
- Completion with original manufacturer information for 100% data quality and orderability, e.g. by product names, product descriptions, EAN, article numbers, type codes, ECLASS IDs, etc.
- Addition of the current product status (active, discontinued) for reduced risks from obsolete spare parts (obsolescence management)
- Transparency of available suppliers thanks to the access to the SPARETECH database
- Direct Interface to ERP System:
Apply changes through change requests directly to the existing material master via interface to your ERP System
Related to the topic
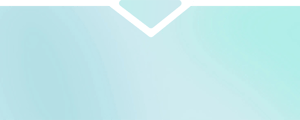
Get started today
SPARETECH is the fastest and most reliable way to reduce inventories and costs in spare parts management.