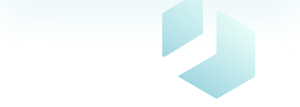
No downtime due to missing spare parts. Never.
Reducing unplanned downtime is crucial to ensure high machine and equipment availability. Yet, finding needed spare parts during a machine failure can be challenging. Discover how reliable spare parts data helps to minimize machine downtime.
How to eliminate unplanned downtime?
One of the main levers to reduce unplanned downtime is to have a proper spare parts data management in place. Having reliable, up-to-date information about spare parts in the system helps to identify needed parts quickly when it comes to unforeseen machine failures.
Insufficient spare parts data quality often leads to unplanned machine downtime, hindering quick repairs and causing operational disruptions.
.png?width=300&name=SPARETECH-favicon%20(1).png)
Software tools automate spare parts management processes which leads to reduced downtimes and increased efficiency during machine failures.

KPIs such as mean time to repair (MTTR) and overall equipment effectiveness (OEE) help to evaluate and continuously improve measures to minimize downtimes.
Identify the root cause for unplanned downtimes
Machine downtime due to missing spare parts, can be attributed to various factors, such as wrong or inadequate spare part information in the ERP system, limited ERP search capabilities yielding no results, and a lack of information about available spare parts within the production network. These issues are all rooted in unreliable and non-transparent spare parts master data.
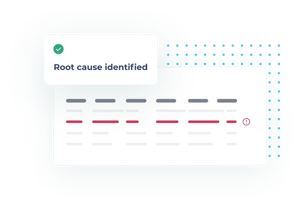
Improve data quality & automate through software
Software tools can massively help to fix the root cause for machine downtimes. SPARETECH detects errors, duplicates and discontinued products in the customer ERP System and enhances it with reliable spare parts data from original manufacturers and suppliers. In combination with an effective search and automated BoM-Checks this enables maintenance teams to find needed spare parts immediately during unexpected failures. The transparency and automation provided by the software speeds up processes from the identification to the ordering of spare parts significantly.
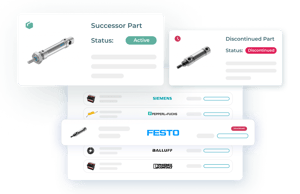
Monitor KPIs and track results
After addressing the root causes of machine downtimes, KPIs and metrics such as Mean-Time-to-Repair (MTR) and Overall Equipment Effectiveness (OEE) should be tracked diligently to see how much time and money could be saved.
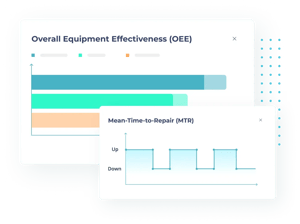
How does SPARETECH work in your daily operations?
- Completion with original manufacturer information for 100% data quality and orderability, e.g. by product names, product descriptions, EAN, article numbers, type codes, ECLASS IDs, etc.
- Addition of the current product status (active, discontinued) for reduced risks from obsolete spare parts (obsolescence management)
- Transparency of available suppliers thanks to the access to the SPARETECH database
- Direct Interface to ERP System:
Apply changes through change requests directly to the existing material master via interface to your ERP System
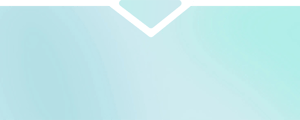
Get started today
SPARETECH is the fastest and most reliable way to reduce inventories and costs in spare parts management.