Data exchange between SPARETECH and ERP systems
With the Digital Workflow in the SPARETECH App you can create new materials or change existing ones in your material master. At the same time you can use Insights you can enrich your data sets with product information as well as obsolescence information directly from the manufacturer.
In order to fully exploit the power of SPARETECH, regular two-way data exchange between the application and your ERP is necessary:
- From SPARETECH to ERP (outbound): To transfer new materials, plant extensions or changes. The latter may also include data enrichments or obsolescence information from the SPARETECH database.
- From ERP to SPARETECH (Inbound): To transfer the material numbers of newly created materials and to ensure that changes made in ERP are also taken into account in SPARETECH.
SPARETECH offers two different options for inbound and outbound data exchange that differ in implementation effort, amount of manual interaction, and frequency of data exchange. This blog post will help you decide if manual or automated data exchange is right for you.
Manual Data Exchange
Manual data exchange is the simplest way to synchronize the data between ERP and SPARETECH. It works with data exchange files in .xlsx or .csv format containing all relevant data. First we consider the outbound (from SPARETECH to ERP).
Outbound Data Exchange
Before the data from new material plants, material changes or plant expansions can be brought into your ERP, a data exchange format must be defined. This is usually an Excel table that contains all the relevant attributes of the material master data records, e.g. manufacturer, manufacturer article number, type code, etc., in a specific sequence so that it can be processed by your ERP. The order of the data is fully configurable to your requirements. All data created in SPARETECH can now be exported in this template. The template could look like this:

Once your data is prepared and exported to a format compatible with your ERP system, you can use it to update the data in your ERP system and synchronize the systems.
Manually entering large amounts of data into an ERP system can be a time-consuming and error-prone task. To avoid this, there are a few ways that bulk upload can be handled in ERP systems, including third-party solutions that focus on automating master data management.
Tip: If you use SAP, we provide an overview of different methods you can use for mass upload / maintenance of material master data. Most of these methods require IT support to set them up properly in your company.
Inbound Data Exchange
Usually material numbers are generated in the ERP system. Therefore it is important to synchronize the data with SPARETECH to ensure that the data is correctly linked to your material master data record. Therefore it is important to also have a data exchange from SAP back to SPARETECH (inbound). This also ensures that any other data changes made in SAP are reflected in the material master in SPARETECH. To do this, simply upload the SAP export of your material master to SPARETECH. The data will then be processed in the background and you will be notified when the update is complete.
Frequency
The frequency of manual data exchange between SPARETECH and your ERP and vice versa can be controlled by the customer and depends on time criticality and frequency of changes.
From SPARETECH to ERP, data is usually transferred either by the person creating or modifying a material as soon as the creation/modification process is completed, or it can be transferred by a central person/team according to a fixed schedule, e.g. daily or every two days.
From ERP to SPARETECH, typical update cycles vary from daily to weekly and are performed by a central person/team.
Requirements
- Relevant master data attributes must be defined
- Data import process into ERP possible (e.g. via MM01, LSMW, Winshuttle/Precisely)
- Update process and responsible persons must be defined
Automated Data Exchange
To avoid manual interaction in daily operations, SPARETECH offers the possibility to exchange data via an API (Automated Process Interface). This allows all material master data created in SPARETECH (new installations, changes, plant expansions, also called material events) to be seamlessly synchronized with your ERP without the need for additional process steps. Updating your material master in SPARETECH also works fully automatically without manual intervention.
To ensure the functioning of the automated data exchange, it is important to follow preparatory steps, such as:
- Define the end-to-end business process, including relevant use cases for integration and relevant fields and attributes to be exchanged between SPARETECH and your system
- Define integration concepts (e.g., high-level architecture, see an example below).
- Coordinate this initiative internally with your central IT team and get buy-in from all relevant stakeholders
Once this preliminary work is completed, you can start the integration project, which includes the following steps:
- Carrying out the necessary configurations and developments
- Perform tests
- Deployment in the production environment
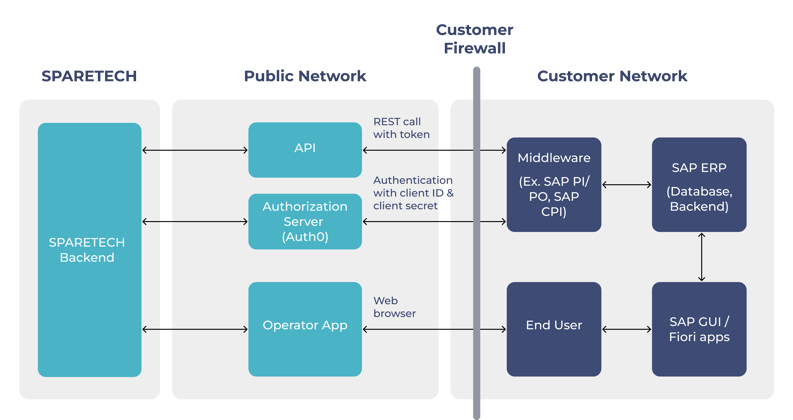
Frequency
The update frequency is entirely up to you and can vary from a few seconds to once per hour or per day.
Want to learn more?
Click here for the blog post about the SPARETECH API and here for the API documentation.
Advantages and Disadvantages
Manual Data Exchange
➕ Low to medium implementation effort
➕ Low to medium implementation time
➕ Flexibility - exchange data whenever you need it
➖ Manual interaction required for data exchange
➖ Latency medium to high
Automated Data Exchange
➕ No manual interaction required
➕ Data synchronization in near real time
➕ Less susceptibility to errors due to lack of manual interaction
➕ Minimal effort for support and maintenance
➕ Scalability
➖ Medium to high implementation time
➖ Requires IT capacity
Summary - What's right for you?
Manual Data Exchange
→ If you want to get started immediately
→ If you have limited IT resources
→ If your data creation is not too time-critical
Automated Data Exchange
→ If you want to avoid manual effort in your day-to-day business
→ When seamless and immediate data transfer is important
→ If you have IT resources at your disposal
Tip: You can start manual data exchange at any time - this is a good basis for later implementation of automated data exchange!