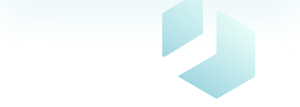
Always up-to-date about discontinuations & successor products
MRO obsolescence management is a proactive approach to identifying and managing the risk of discontinued parts. By getting all manufacturer announcements of discontinuations, and the successor product in one dashboard, obsolescence management is easier than ever before.




Why is efficient obsolescence management crucial?

Production downtimes cause significant costs, especially if they are caused by discontinued parts that are not available in stock or among suppliers. Using alternative sources of supply often leads to longer delivery times, higher costs and additional effort.
Proactive discontinuation management avoids the high costs of procuring discontinued spare parts. Instead, critical parts can be ordered early or, thanks to successor and supplier information, procured when needed at the best price and shortest delivery time.

The larger the production facilities get, the more complex it becomes to track and maintain MRO data. As a result, many maintenance teams find it difficult to keep track of discontinuations and successor information that is sent out by many suppliers via a wide variety of channels.

Dependence on global supply chains for components can make it difficult to procure obsolete MRO spare parts. Transparency regarding the availability of spare parts in the company's own production network and from suppliers worldwide can resolve individual supply chain disruptions.
Keep track of discontinued products with ease
When a manufacturer stops making and selling a particular spare part, it's because there's new technology, less demand, or a better product. With SPARETECH's app, you can easily track when this happens to the parts you use. Get the latest updates and prepare for any changes ahead of time.
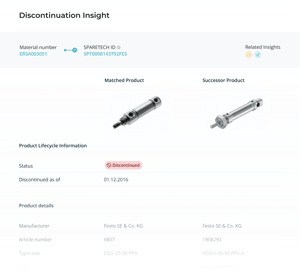
Source parts within and beyond your network
The information about successor products are sourced directly from our partners like Festo, Bosch Rexroth, and many others. This way you can check at any time, which product is available to substitute the discontinued part. Utilizing SPARETECH's data you are always up-to-date and keep track of the successor products you might need in the event of a machine failure.
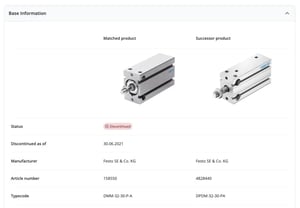
Get information about the successor parts you need
- Access 100% complete and up-to-date original manufacturer information.
- Easily compare procurement possibilities for identical parts.
- Ensure efficient cross-plant collaboration through one single source of truth and save unnecessary procurement costs and storage space.
Related to the topic
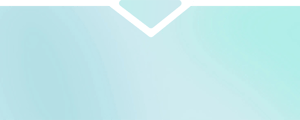
Get started today
SPARETECH is the fastest and most reliable way to reduce inventories and costs in spare parts management.