Seamless data exchange workflow with SAP via SPARETECH API
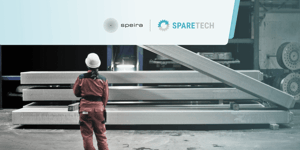
About Speira
Speira is a leading European aluminum rolling and recycling company with eleven production sites across Germany and Norway. With operating facilities like Grevenbroich (the world's largest refining plant), Hamburg, and Neuss, the company processes around one million tons of advanced rolled products annually, serving key industrial sectors, including automotive, engineering, and construction.
The company relies on SPARETECH software to enhance spare parts management and further increase operational efficiency and effectiveness.
Time Savings
Reduced material creation time from 20-30 minutes to just 5 minutes per item.
Process Optimization
Standardized workflows across all three plants with seamless SAP integration.
Data Quality
Improved master data quality with automated duplicate checking and manufacturer data enrichment.
Introduction
Efficient MRO spare parts management can make the difference between smooth operations and costly downtime, offering manufacturing companies considerable savings - both financially and in terms of processes.
With operations spread across multiple locations in Germany and managing over 72,000 master records for spare parts and auxiliary materials, Speira faced significant challenges in achieving and maintaining spare parts data quality and standardizing its process across plants.
Their collaboration with SPARETECH, particularly in implementing a seamless data exchange with SAP via the SPARETECH API, demonstrates how MRO software can significantly impact traditional spare parts management practices.
Challenges in spare parts management
Speira needed to streamline its spare parts management across multiple plants. The Spare Parts team relied on Excel file exchanges to maintain master data records, which required extensive manual effort given their operational scope:
- Maintain database of 72,000 master records covering spare parts and supplies
- Process approximately 2,500 spare part repairs annually
- Handle around 1,500 new material creations yearly
- Manage roughly 500 procurement orders
- Process about 750 devaluation cases
The team encountered several key challenges:
- Lack of standardized procedures: The absence of standardized procedures across different locations hindered operational efficiency.
- High manual workload: The reliance on manual data management and the exchange of Excel files led to increased workloads and error susceptibility.
- Poor master data quality: The lack of a streamlined process resulted in duplicate entries and inconsistencies in the spare parts master data.
- Limited standardization in procurement processes due to the historically grown SAP material maintenance in long text fields
- Time-intensive processes: Creating new material entries was lengthy, taking an average of 20-30 minutes per entry.
As a result, Speira's priorities became:
- Coordinating spare parts management across their three plants in Hamburg, Neuss, and Grevenbroich
- Ensuring and improving data quality and preventing duplicate entries in their master data
- Implementing standardized digital workflows for spare parts management
The approach: Seamless data exchange with SAP via API
SPARETECH implemented a comprehensive spare parts management solution with full SAP integration via API. This powerful automated data exchange between SPARETECH and SAP eliminates the need for manual data export and import between systems. With real-time updates of spare parts data from the SPARETECH app to the ERP system and back, Speira optimizes its spare parts creation and data enrichment processes.
- Standardized digital workflows for material creation and management
- Efficient master data enrichment with data that comes directly from manufacturers
- Automated duplicate checking across all plants
- Streamlined synchronization between SPARETECH and SAP systems
Implementation
The implementation process was completed within 2-3 months, featuring:
- Full integration of SPARETECH with SAP MM module via API
- Custom workflow configuration aligned with Speira's specific needs
- Middleware setup for seamless data exchange
- User training and role-based access configuration
"Through SPARETECH and our agreements, we've grown together as a company. We meet regularly, coordinate more effectively, and work much more harmoniously across our plants."
Bernd Schäfer
Spare Parts Manager | Speira
Results & Benefits
The introduction of the SPARETECH app enabled seamless data exchange with the SAP system, significantly reducing manual effort and delivering significant improvements in Speira's spare parts management:
Standardized processes
Operations across Germany now follow a more harmonized approach to master record processes through seamless SAP integration. This standardization improves workflow efficiency and plant collaboration.
"The integration has allowed us to work much more harmoniously and standardized across our processes related to master data."
Bernd Schäfer
Spare Parts Manager | Speira
Faster material creation processes
The standardized processes have dramatically improved efficiency in creating new materials, cutting data entry time from 20-30 minutes to just five minutes per entry.
"Previously, creating a new entry took 20-30 minutes, but now, with SPARETECH, it takes just five minutes."
Bernd Schäfer
Spare Parts Manager | Speira
Efficient spare parts data management
With SPARETECH and its direct interface to SAP, data can be sourced directly from manufacturers and entered into Speira’s system, reducing manual entries and duplicate records. Additionally, the consistent formatting makes orders more readable for suppliers, streamlining spare parts management.
These improvements in data management and process standardization have created a strong foundation for major MRO optimizations. In particular, Speira has achieved significant inventory optimization results.
"SPARETECH enabled us to reduce our spare parts inventory by €135,000 at the push of a button."
Friedhelm Iske
Former Head of Strategy & Technology | Speira
"Over the past three years, we’ve accomplished a lot together, including being the first customer to fully leverage the interface. Now that the API is fully operational, we’re excited to continue our collaboration and realize its full potential, driving consistent, high-quality data across the master data.”
Paula Rückel
Customer Success Manager | SPARETECH
By implementing SPARETECH with full SAP integration, Speira has transformed its spare parts management process, achieving greater efficiency, standardization, and collaboration across its plants. The solution has improved their operational efficiency, enhanced data quality, and reduced manual workload.
The successful implementation demonstrates that a well-thought-out interface integration boosts efficiency and lays the foundation for a future-proof business strategy.
Webinar Recording 🖥️
Watch the webinar recording to get first-hand insights into how Speira has improved its spare parts management practices with SPARETECH.
FAQs: The SPARETECH API
🌀 Which departments use the tool at Speira?
At Speira, the SPARETECH tool is primarily used by the spare parts department, which decides which parts to stock in the inventory.
🌀 Can items be created without manufacturer information?
Yes, this is possible. While our database currently contains only manufacturer-specific parts, you can make the manufacturer field optional. If your company’s SAP configuration doesn't require manufacturer information, you can create parts without it—this won't cause any issues on our end.
🌀 What field is the SPARETECH ID transferred to in SAP?
For Speira, we created two classification fields: One for the SPARETECH ID and one for the Creation ID.
🌀 How long does the integration of SPARETECH with SAP take?
Depending on the company's IT setup, reaching error-free operation usually takes 2 to 3 months.
🌀 What does the SAP S/4 Public Cloud integration look like? Do I need additional middleware, and can I integrate directly via API?
From our side, as SPARETECH, we offer a set of API endpoints that use JSON to transfer the data. You can definitely integrate with our APIs if your system is capable of:
- Call an endpoint.
- Understanding JSON.
- Parse JSON to the appropriate format.
- Map JSON keys to the corresponding MM fields.
🌀 If SAP provides standard APIs (which it does), why do you not integrate those?
We want to support customers using all ERP systems, not just SAP. Our current setup allows for that flexibility.
🌀 Why is the data not pushed from SPARETECH to SAP?
As of now, our system offers a set of API endpoints to pull the changes constantly. We are working on a solution to push changes near real-time via webhooks. This capability will eventually be part of our system
🌀 Are sync errors only displayed for material changes or also for material creations?
Sync errors are displayed for both.
🌀 How does the SAP material number assignment work through the middleware?
The material number assignment can be structured similarly to how SAP or the ERP currently assigns it. There is flexibility on your side to restrict this generation to a certain number ranges or similar. Overall, the assignment of material numbers lies completely on the ERP system side
🌀 Is the eClass transferred to SAP in addition to the selected material group?
Yes, the eClass is transferred to SAP in addition to the selected material group. Some customers also use the standard field External Material Group to adopt the eClass information if this field is not already being used internally for other purposes. This approach allows for better classification and organization of materials within the SAP system.
🌀 Can the programming effort be estimated here in hours?
The short answer is "no." We had very few customers with a wide variety of experiences to give a meaningful number. Factors that affect the integration effort are their experience with integrations, how many material master fields need configuration and mapping, and whether the development is internal or external.
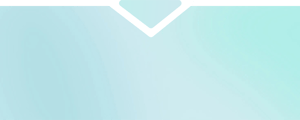
Get started today
SPARETECH is the fastest and most reliable way to reduce inventories and costs in spare parts management.