Slashing spare parts inventories
.png?width=300&name=Case%20Study_Header%20Image_2000x%201000_Idahoan%20(1).png)
About Idahoan Foods
Founded nearly 60 years ago, Idahoan Foods is a leading manufacturer of packaged potato products, including mashed potatoes, hash browns, and casseroles. The company generates annual sales of $750 million and operates three manufacturing facilities based in Idaho Falls.
Managing over 13.5K SKUs, Idahoan Foods has partnered with SPARETECH in 2024 to optimize MRO inventory management and spending, ensuring smooth operations throughout its expanding manufacturing facility.
Initial situation: Challenges in MRO inventories and spend
Idahoan Foods operates three manufacturing plants in Idaho, with one facility undergoing expansion. Previously, these plants functioned independently, managing separate spare parts inventories with little coordination. This siloed approach—combined with rapid growth and frequent changes in the maintenance system—created significant challenges in managing MRO inventory across all locations. The company faced the following challenges:
Lack of data accuracy and standardization
The absence of a dedicated master data manager and consistent data entry standards led to significant data quality problems across the system, such as inconsistent part naming conventions and descriptions. This often led to inaccurate data or duplicate entries of the same parts under different supplier numbers, limiting inventory and spend visibility.
Operational pressure on inventory management
Idaho Falls is a relatively isolated area, which presents sourcing challenges. As a company with nonstop operations, it maintained higher-than-recommended inventory levels, including non-critical spares, to mitigate the risk of downtime. This operational intensity created a constant challenge of balancing inventory levels with the need for reliable equipment performance.
As a result, a substantial portion of the inventory remained unused. After engaging with SPARETECH, it became evident that nearly 50% of the inventory had not turned over in three years. Out of 13,000 SKUs, only around 6,500 to 7,000 were actively used.
Lack of visibility into obsolete spare parts
Another key challenge was the accumulation of obsolete spare parts in the inventory. After discovering that 50% of their stock had not turned over in three years, the team conducted a preliminary review and immediately identified that 10% of those items were obsolete. These parts were linked to equipment that had been replaced or removed during facility upgrades and expansions. Without a structured process for managing obsolete inventory, these outdated parts took up space and resources.
Solution implementation: SPARETECH MRO software
To address these challenges, Idahoan Foods implemented SPARETECH's MRO software, providing access to 30 million unique spare parts catalog entries with AI-powered search and cross-referencing capabilities. The implementation began with thorough spare parts data analysis and cleansing, followed by full data exchange into their ERP system.
The company has leveraged key features, including duplicate detection, obsolescence recommendations based on manufacturers' original information, and standardized part descriptions across plants.
Implementation process
The implementation process followed these steps:
- A proof of value (PoV) consisting of an initial data export from the ERP system, delivering first results within 30 days.
- After the successful PoV, we aligned on data exchange & migration setup.
- User adoption strategy, including an on-site visit to Idahoan Foods' facilities:
- Consolidated and standardized part creation to ensure data consistency
- Provided web-based interface access to maintenance and procurement teams
- Full data exchange with existing system landscape, Microsoft Dynamics 365 ERP system
"SPARETECH's efficiency was remarkable. We provided our spare parts data, they analyzed it, came back to us and gave us preliminary results even before we finalized the contract. The moment we signed, we had immediate access to actionable results that we could implement right away."
Jim Devenney
Procurement Manager | Idahoan Foods
Key outcomes: MRO inventories and spend optimization
Through the first year of collaboration with SPARETECH, Idahoan Foods has significantly improved MRO data quality, reduced inventory levels, enhanced operational efficiency across plants, and created a more transparent procurement process.
Inventory optimization
- Identified approximately $3 million worth of unused inventory over a 3.5-year period
- Eliminated about $500,000 in obsolete parts after the first analysis
- Inventory reduction of 50% for common parts across locations identified
We identified approximately $3 million worth of unused inventory over a 3.5-year period. In our first pass alone, we eliminated around $500,000 in obsolete parts.
Jim Devenney
Procurement Manager | Idahoan Foods
Data quality improvements
- Consolidated part creation on the SPARETECH system to maintain data consistency
- Elimination of duplicate entries through live AI-powered duplicate check
- Standardized part descriptions across all three facilities
"We've streamlined our MRO data management. Instead of directly creating parts in our ERP system, we first consult SPARETECH, which instantly identifies if we already have the part and provides all the necessary information. This allows us to efficiently tie parts to additional assets or locations and create products within our ERP with complete confidence in the data quality. This approach, combined with constant duplicate checking, has dramatically improved our inventory and procurement decisions."
Jim Devenney
Procurement Manager | Idahoan Foods
Operational efficiency
- Successfully integrated with Microsoft Dynamics 365 ERP system
- Improved part identification and retrieval process across all three manufacturing facilities
- Enhanced ability to identify and plan for obsolete parts with replacement options
"The amount of work and the accuracy that it changed in our system is outstanding. We actually know what inventory we have now. We know what part it is, we know on which facility it is. We know how many we have and if we use it, which is a huge step forward for us."
Jim Devenney
Procurement Manager | Idahoan Foods
Future outlook: Further MRO optimization with AI-powered software
Looking ahead, Idahoan Foods plans to enhance its integration with SPARETECH by implementing a streamlined part request workflow. Maintenance teams will be able to request new parts directly through SPARETECH, which will automatically flow through an approval process and integrate into the inventory system, eliminating manual data entry and reducing the potential for errors.
- Implementing data exchange with their ERP system to streamline operations
- Long-term partnership goals
- Continue optimizing inventory management across all three facilities
- Further standardize data entry and part creation processes
“There's still a lot of manual work in the factories today, including data entry and error-prone processes. While humans will always remain at the center of decision-making, we now have much better tools to orchestrate these decisions, ultimately leading to global collaboration.”
Martin Weber
CEO | SPARETECH
Webinar Recording 🖥️
Watch the webinar recording to learn more about how SPARETECH supports Idahoan Foods with AI tools to slash spare parts inventories.
FAQs
🌀 How does SPARETECH integrate with existing systems?
- SPARETECH is ERP agnostic.
- It integrates with all major systems, including SAP, Oracle, IBM, and Microsoft Dynamics.
- About 80% of the customer base runs on SAP, 20% on other MRP systems.
- Integration is done through API, described as a "painless process".
🌀 How long does it take to see the first results?
- Results are instantaneous once system access is granted.
- Idahoan Foods received preliminary results before signing the contract.
- Continuous results depend on the implementation schedule.
🌀 What are the sources of data used by the software to identify discontinued or obsolete items?
- The software only uses verified data from original manufacturers.
- It won't display discontinued information from third-party websites.
- It considers the manufacturer as the only trusted source.
- It verifies data before marking items as obsolete.
🌀 Are there various profiles set up for different departments?
- The system has different roles and permissions.
- It includes access for the spare parts department, engineering, procurement, and production.
- Project work can be separated from day-to-day operations.
- Users can see inventory status and perform sourcing actions based on their role.
🌀 How did you handle the SPARETECH LLM learning all vendors and part numbers?
- SPARETECH has been in the market for 6 years.
- It has been using machine learning since the beginning.
- It contains over 30 million parts in the database.
- It is continuously growing through partnerships with manufacturers and suppliers.
🌀 What MRP system is Idahoan Foods using, and how did you handle integration?
- Idahoan Foods uses Microsoft Dynamics 365.
- Integration was done through data exchange.
- A SPARETECH team member collaborated to map fields.
- Process is described as straightforward despite typical ERP integration challenges.
🌀 Can engineers purchase a part for a project that later becomes a spare part?
Yes, users can look up parts in SPARETECH.
- Users can make product requests through the system.
- There is the option to purchase as a non-inventoried item or convert to a spare part.
- Requests flow through an approval process.
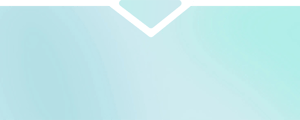
Get started today
SPARETECH is the fastest and most reliable way to reduce inventories and costs in spare parts management.