Manufacturing companies want to avoid unplanned plant downtime at all costs, as the availability of this equipment is a critical success factor for them. For this reason, they keep large quantities of spare parts in their warehouses to be able to react in the event of a machine failure. This is reflected in high costs for procurement and warehousing, even though 41% of spare parts are never used and end up scrapped. SPARETECH provides transparency in spare parts management and links by intelligent matching algorithms the master data of the customers available in the ERP systems with more than 10 million data records of the SPARETECH database coming from original equipment manufacturers.
This intelligent linking of data enables manufacturing companies to cleanse their master data, identify duplicates and stay informed about discontinuations. In addition, procurement sources become transparent and cross-company pooling concepts are made possible. This collaborative approach of a pooling concept has the concrete advantage for our customers that they only purchase the spare parts that are really needed (spare parts availability as-a-service).
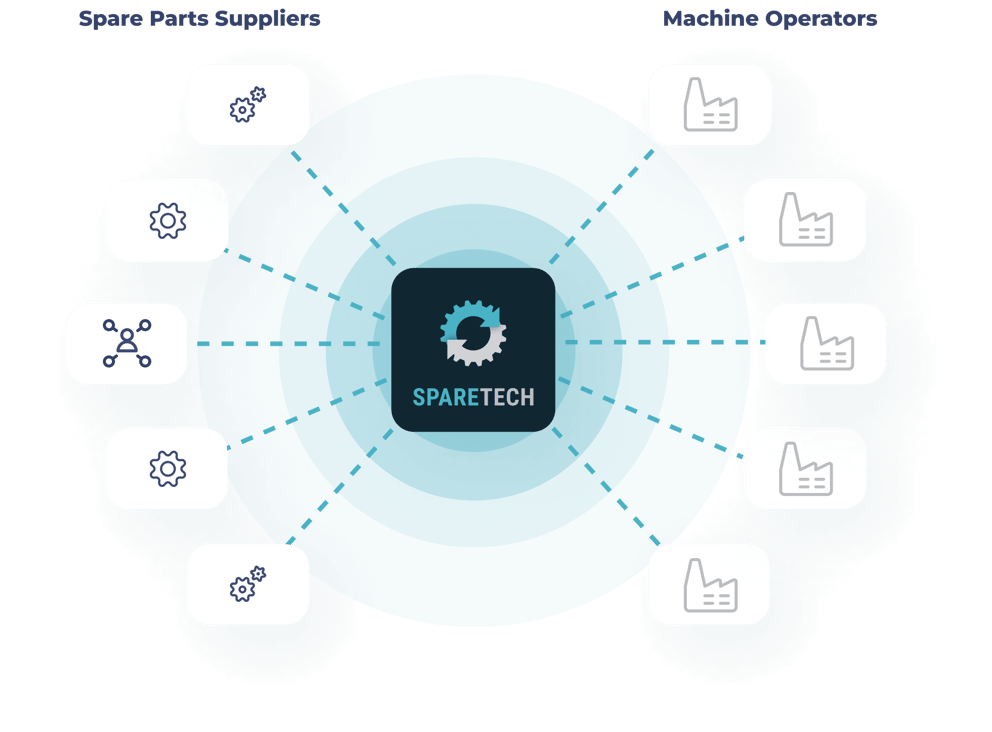
The problem
Spare parts management for machinery and equipment is increasingly a challenge for manufacturing companies. SPARETECH analyses show that the average inventory of a globally operating industrial company amounts to more than 109 million euros and increases by up to 12 percent annually. Plant operators see this spare parts inventory as a kind of physical insurance to be able to react quickly in case of a plant failure. Up to now, there has been no transparent data on which spare parts are available at which location. This is despite the fact that the common parts rate at many companies is 15 to 25 percent - in some cases even over 40 percent. This is mainly due to poor data quality: up to two thirds of all data records in the ERP system are incorrect. Typical sources of error are missing information, inconsistent notations, hidden duplicates or recoded data records.
The inconsistencies in the spare parts master data make it more costly to consolidate inventories and reduce procurement costs. The poor data quality in the material masters of the various locations also makes it difficult to perform a needs-based analysis of spare parts, to integrate plant scopes, and to create new spare parts without duplicates. Language differences, different data formats and structures pose additional challenges and complexity drivers, especially for globally positioned suppliers.
Our customer analyses show that even a single automotive plant stores an average of €42 million in spare parts. However, only 20% of this is needed per year. 41% of the spare parts are even never used in the life cycle of the plant and have to be scrapped unused. The scrapping of spare parts not only costs hundreds of thousands of euros per plant every year, at the same time it is an ecological disaster: resources, energy, transport routes in global supply chains, manual handling steps are wasted without further value creation.
The problems can be summarized as follows:
- High inventories and associated capital commitment costs
- Machine downtime due to inefficient search & intransparency
- High procurement costs for spare parts
- High manual personnel expenditure for warehouse and master data management
- Ecological waste due to scrapping of unused spare parts
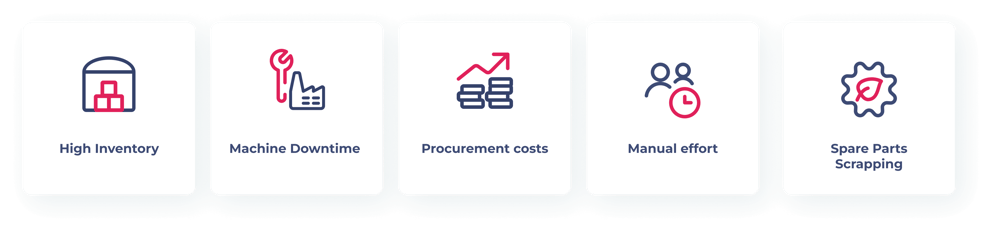
The solution
To meet the challenges described above, SPARETECH offers a reliable digital data platform for industrial spare parts. The SPARETECH software automates processes from identification to checking of spare parts availability and covers the entire life cycle, starting from the original production of the spare part at the original manufacturer, through to scrapping (end-of-life). The basis for this is SPARETECH's cross-industry and independent product database for machine spare parts - which contains over 10 million products from thousands of original manufacturers, dealers and distributors.
In the first step, the software uniquely identifies the spare parts. State-of-the-art technologies from the fields of semantic data management, big data and automated data processing are used here. In the second step, duplicates, discontinuations and common parts across locations are made visible and original manufacturer product information is added. This creates a complete and error-free database that makes it possible to address the cross-company pooling concept described at the beginning.
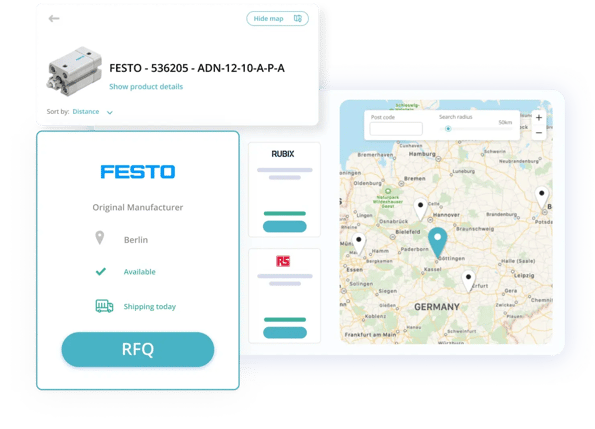
Spare parts pooling with SPARETECH & Leadec
The database described above is the basic prerequisite for setting up a cross-site warehouse management system in which several plants access a central spare parts warehouse. This approach can significantly reduce inventories and cut costs. Ensuring the availability of spare parts is also a top priority under this approach. In an initial pilot project with a globally active automotive supplier, a common parts analysis identified an inventory value potential in the 7-digit range to be outsourced. Here, Leadec is contributing its expertise in in-plant logistics and maintenance from daily work in more than 300 factories worldwide. From 2023, the next step will be for several companies to source a relevant spare parts requirement from a central warehouse - which will significantly reduce the costs per company.
"Spare parts procurement can become even more flexible when several companies access a spare parts pool. The spare parts are supplied on demand and financing models, so-called off-balancing, can significantly reduce the capital tied up," says Stephan Hihn, who heads product management for Leadec in Europe.
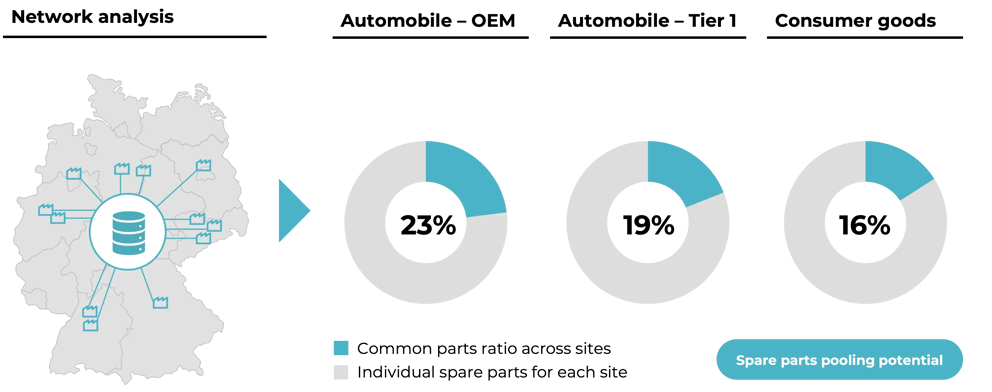
Pioneers wanted
Take your spare parts management to the next level. For the pilot project with Leadec, we offer a free quick check for companies that are in the following initial situation:
- Decentralized production network with locations in Europe
- Production plants and production lines with high availability requirements
- Interest in off-balancing and physically outsourcing their production spares
- The physical spare parts warehouse is to be digitized and inventories optimized
The focus of the pilot project is on high-priced, slow-moving spare parts within complex and highly automated production lines.