In today's data-driven world, data quality is becoming increasingly important for spare parts management. Poor quality data in the material master can lead to inaccurate reporting, high inventory levels, and decreased efficiency.
💡 Data quality refers to data accuracy, completeness, and consistency.
With organizations being focused on process improvements and cost reductions, clean, duplicate-free master data is crucial for efficient day-to-day activities. Manufacturing companies today are facing growing pressure to make data-driven decisions to remain competitive. The ability to trust the data used to make these decisions is paramount. Therefore, ensuring high-quality data is essential in order to gain a competitive edge.
How do you tackle poor data quality once you've identified it? What is its impact on spare parts management processes? We have compiled answers to these and other questions below.
How to tackle poor data quality once identified? What is its impact on spare parts management processes? Find the answers to these and more questions below.
The challenge: Poor data quality in the material master
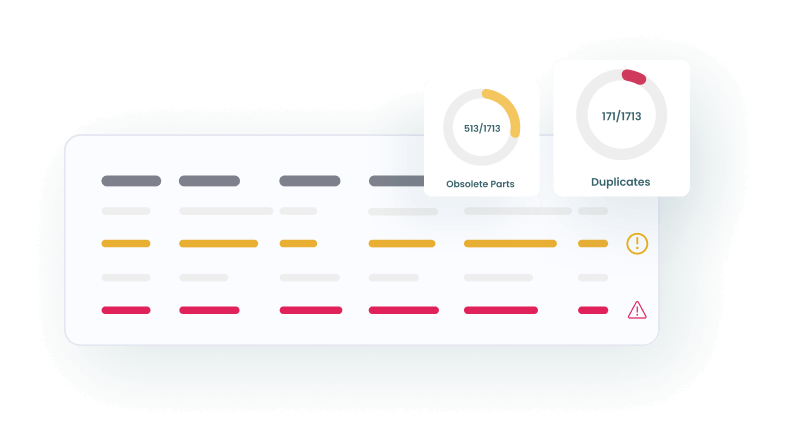
Ensuring efficient, reliable, and collaborative processes is not always a straightforward path for maintenance personnel. One of the major challenges they face is poor data quality in the material master. This can manifest in different ways, including:
- Data duplicates
- Data obsolescence
- Data inaccuracies
- Incomplete information
Knowing the origin of poor data quality is crucial for comprehensive and continuous data cleansing. These causes must be eliminated sustainably through standardized processes and with the help of software solutions in order to ensure correct and complete master data.
Causes of poor data quality
Once the existence of poor-quality data in the material master has been identified, the next step is to understand where the problem is coming from. Only then can it be tackled.
Below are some of the main causes for each of the types of poor data listed above:
- Data duplicates: can often arise from multiple and international production locations, as well as due to human error.
- Data obsolescence: can result from discontinued products that remain in the system or outdated information.
- Data inaccuracies: can result from incorrect data entry or insufficient validation processes.
- Incomplete information: filling all fields of information can be time-consuming as maintainers often do not have all the necessary information at hand when creating products in the ERP system.
Further causes of poor quality in the material master are:
Outdated legacy systems
Many organizations have been using these systems for years, and over time, they become more difficult to maintain and update. As a result, data can become siloed, redundant, and inaccurate.
Lack of integration between different systems
This can lead to data inconsistency, especially when data is being manually entered or transferred between systems generating a significant amount of time spent on data cleaning and consolidation. Thereby, reducing efficiency and increasing the likelihood of errors.
Lack of data governance and data ownership
These factors can also contribute to poor data quality in the material master. Without clear guidelines and ownership of data, it can be difficult to ensure consistency and accuracy. This can result in data being entered inconsistently or in different formats, leading to duplicate or inaccurate data.
Tackling these causes is crucial to ensuring accurate and reliable data for decision-making purposes.
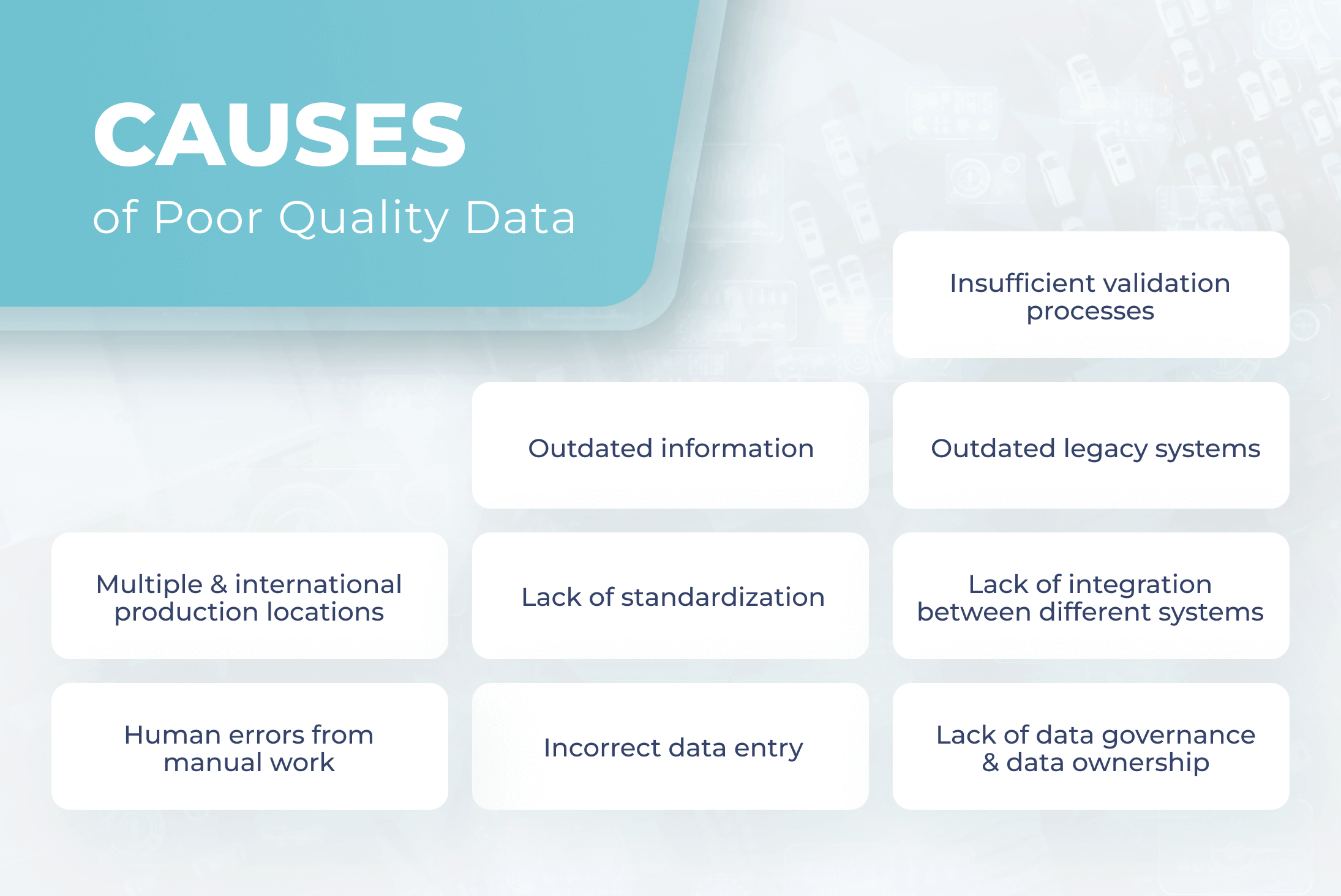
Consequences of poor quality data
The existence of inaccurate, incomplete, and outdated data results in a lack of transparency and uninformed decision-making within organizations. One of the main consequences of poor data in manufacturing companies is excess inventory levels. Inaccurate data can make it difficult for manufacturers to forecast demand and plan for procurement, thereby leading to overstocking of certain items, which can tie up capital and increase storage costs, or understocking necessary spare parts, leading to costly delays in maintenance and repairs.
Additionally, poor data quality can lead to high machine downtimes as a result of incorrect maintenance planning and scheduling or a lack of spare parts. This causes increased production costs and reduced productivity. As a result, high procurement costs, low ROI, and high CO2 emissions are generated.
How to ensure high-quality data in the material master?
The challenges of poor data quality in the material master can be effectively tackled through the use of software solutions. By automating material creation and identification processes, software solutions can reduce the risk of human error and ensure standardization across different systems. They can also perform real-time data quality checks to identify and clean up data duplicates, inaccuracies, and redundancies. This, in turn, leads to clean, duplicate-free master data that can be trusted for decision-making purposes. By addressing the causes of poor data quality and leveraging software solutions, companies can improve their data-driven decision-making, gain a competitive edge, and increase their bottom line.
One such solution is SPARETECH, the leading data platform for industrial spare parts that leverages the latest technologies from semantic data processing and big data to streamline spare parts management. SPARETECH identifies and cleans duplicates and discontinuations in the material master and provides valuable insights based on the matching with the global spare parts database covering over 12M products from 5,000+ suppliers.
Manufacturing companies such as ElringKlinger and WEPA have optimized their spare parts management processes by using SPARETECH software. You can learn more about our success stories in the following blog articles:
- Best Practice: Master data management of duplicates
- Webinar with ElringKlinger: Transparency in the Material Master
If you are struggling with poor data quality, do not hesitate to contact us. We are ready to help.